Hardwood Construction
Experience the difference with individually handcrafted hardwood floors.
Hallmark Floors uses FSC® hardwood veneers and Carb II complaint glues for the center-ply in our engineered floors’ hardwood construction. The center veneers are cold pressed, then hot pressed with tremendous pressure. This process makes the center core Eco-friendly, harder and more proportionally stable.
- Higher Stability
- Higher Density
- Higher Strength
- Higher Indoor Air Quality
Truecore® is third party verified and surpasses the emission requirements.
Sawn-Cut Style
Experts in the industry agree that sawn-cut provides the best quality, stability & visuals for solid & engineered floors. Sawn-cut engineered floors allow for the thickest veneer (4mm) with the highest degree of stability. Engineered sawn-cut wear layers are the ONLY engineered floors that are equal to solid wood floors.
Sawn-cut is made by cutting the log into thick blanks and then set on edge and sent through a multi blade saw, so that the slices are more perpendicular to the growth rings. This process creates a beautiful wood grain and higher quality product, which is unique to sawn-cut face floors.
Collections featuring the Sawn-Cut Face Technique:
Hallmark Floors’ engineered hardwood floors is constructed with an ultra thick wear layer has the same usable surface as 3/4” solid hardwood flooring, this allows 3 guaranteed sandings.
Sawn-Cut Engineered Floors
Superior Wear Layer
Hallmark Floors’ hybrid sawn cut engineered wood floors feature the same wear layer as solid.
Slice-Cut Style
Slice-cut features the same beautiful look as sawn cut veneers and is the second most common way to create a wood veneer, it’s just in thinner layers (2mm or less). This creates stunning visuals while still providing stability for engineered wood floors.
How the wood is cut makes a difference in sliced engineered floors. According to experts, in order to produce a better slice-cut veneer, the log should be vertically cut from the top down. As a result, this creates less stress on the veneer during the slicing process and makes the veneer stronger and provides max stability for a variety of environments. For this reason, Hallmark Floors only vertically slice-cuts the wood used for our floors.
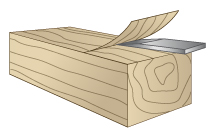
Collections featuring the Slice-Cut Face Technique:
Hallmark Floors engineered hardwood floors feature a 2mm slice cut face layer. This thick wear layer makes it possible to perform 2 guaranteed sandings.
TrueSlice is a new progressive process developed for the sole purpose of greatly increasing one “Stability”. With a highly stable & thicker face cut TrueSlice greatly reduces the opportunity for checking in dry environments when compared to traditional processing methods.
Rotary-Cut Style
The rotary style has a completely different look than sawn-cut. Rotary-cut top layers accentuate the natural grain pattern and have a more pronounced appearance. The random grain visuals are a reflection of how the wood is processed.
Traditional rotary peeled veneers are thinner (2.0mm or less). Spinning the log and peeling off a continuous sheet creates this veneer. Hallmark Floors’ rotary-cut veneers are thicker than industry standards (2.5mm), which gives rotary-cut a more substantial wear surface. Our sophisticated, state-of-the art cutting machinery, careful management of logs, and slow drying process of the veneer, takes Hallmark Floors’ rotary-cut style to a higher performance level than ever before, creating a superior product.
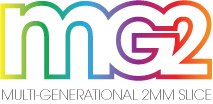
Hallmark Floors engineered hardwood floors feature a 2mm slice cut face layer. This thick wear layer makes it possible to perform 2 guaranteed sandings.
Hardwood Construction | Hardwood 101 Education
You will find the different wood educational categories in the sidebar to the right or if you are on a mobile phone, at the bottom below.